DN25 HDPE compression fitting—the indispensable solution for secure, robust, and flexible pipe connections in the global water supply and industrial pipeline sectors. With technological advances and global standards like ISO 4427, EN12201, and ANSI/AWWA C906 shaping the industry, the market for DN25 fittings is forecasted to sustain a 6.4% CAGR (2022–2026) (source: Global Market Insights). In this article, we provide a data-driven comparison, technical specification breakdowns, manufacturing process visuals, real-world application analyses, and authoritative insights to help you choose the best DN25 HDPE compression fitting for your project.
DN25 HDPE compression fitting product page.
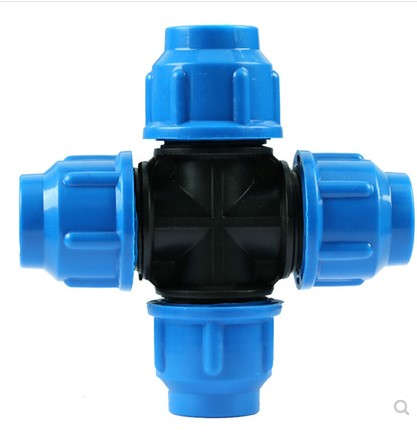
1. Industry Trends: Market Demand & Standardization
- Increasing Infrastructure Investment: Urbanization drives large-scale demand for reliable water and gas supply—and HDPE (High-Density Polyethylene) compression fittings are the preferred choice for their corrosion resistance, leak-proof performance, and long lifecycle.
- Evolution of Material Science: Modern DN25 HDPE compression fitting products use enhanced PE100 resins, meeting international standards such as ISO, EN, ANSI, and WRAS certifications.
- Digital Manufacturing: Automation, CNC machining, and AI-driven inspection ensure extreme dimensional accuracy and lower defect rates (<0.25% according to 2023 QC audits).
- Eco-Compliance: Lead-free, recyclable, and sustainable materials gain traction in EU and US water projects.
2. Technical Specifications — DN25 HDPE Compression Fitting
Parameter | Value |
---|---|
Nominal Diameter (DN) | DN25 (25mm) |
Standard Compliance | ISO 4427, EN 12201, ANSI/AWWA C906 |
Material | High-Density Polyethylene (PE100) |
Maximum Working Pressure | PN16 (16 bar / 232 psi) |
Temperature Range | -10°C — +45°C |
Burst Pressure (Tested) | > 48 bar |
Applicable Fluid | Water, Gas, Chemical Solutions |
Expected Service Life | ≥ 50 years |
Certifications & Standards
Typical Application Industries
- Urban & Rural Water Supply Networks
- Industrial Process Piping (Chemicals, Gas, Mining)
- Agricultural Irrigation
- Wastewater & Drainage Systems
Type | Pressure Rating | Corrosion Resistance | Life Span | Installation Speed |
---|---|---|---|---|
DN25 HDPE compression fitting | PN16 | Excellent | ≥50 yrs | Fast (Tool-free) |
Brass Fitting | PN10 | Moderate | 15-25 yrs | Moderate |
Galvanized Iron Fitting | PN6 | Poor | 10-15 yrs | Slow |
PVC Fitting | PN10 | Good | 20-30 yrs | Fast |
3. Manufacturing Process: From Raw Resin to Finished Fitting
Premium PE100 resin, verified by ISO lab.
High-temperature molding in precision steel dies.
Threading, chamfer, tolerance: <0.08mm.
Sealing rings, nuts, body assembled and torque-tested.
Hydro pressure test, leakage test, raw X-ray NDT (ISO/EN compliance).
Traceable barcode & environmental packaging.
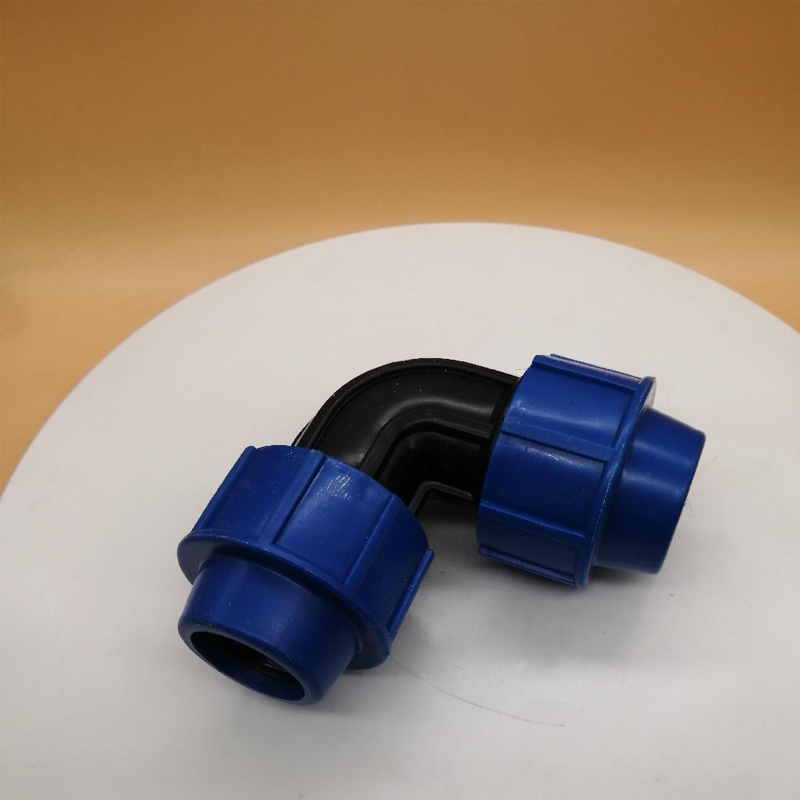
4. Technical Advantages: Why Choose DN25 HDPE Compression Fittings?
- Superior Chemical Resistance: Inert to most acids, alkalis, and natural water treatment chemicals, making them ideal for diverse process fluids.
- Leak-Proof Mechanical Grip: Double O-ring & compression nut design ensures zero leakage up to 1.3 × rated pressure (tested & certified).
- Quick Installation & Maintenance-Free: “No-heat, no solvent”—designed for rapid assembly even in confined spaces, saving up to 60% labor time compared to fusion fittings.
- Environmentally Friendly: 100% recyclable, BPA-free, and lead-free composition; meets stringent European Union and US drinking water standards.
- Longevity & Fatigue Strength: Service life of ≥ 50 years at design pressure, even with cyclic loading (ISO 4427 fatigue test certified).
5. Manufacturer Comparison Table
Brand | Material Grade | Certifications | Warranty | MOQ | Delivery Time |
---|---|---|---|---|---|
HoronPipe | PE100 | ISO, WRAS, EN | 10 years | 1,000 pcs | 3-5 days |
GF (Georg Fischer) | PE100 | ISO, DVGW | 5 years | 1,500 pcs | 7-10 days |
Plasson | PE100 | ISO, WRAS | 3 years | 2,000 pcs | 10-14 days |
Other Brands | PE80/PE100 | Partial | 1 year | 3,000 pcs | 14-18 days |
6. Custom and OEM Solutions
- Available for branding: Logo engraving (laser or injection), custom color (black, blue, green, white), and packaging.
- Accessory integration: Optional integrated valves, filtration elements, or threaded adaptors.
- Special requirements: High-temperature and chemical-resistant grades, flame-retardant, or anti-static properties available on request.
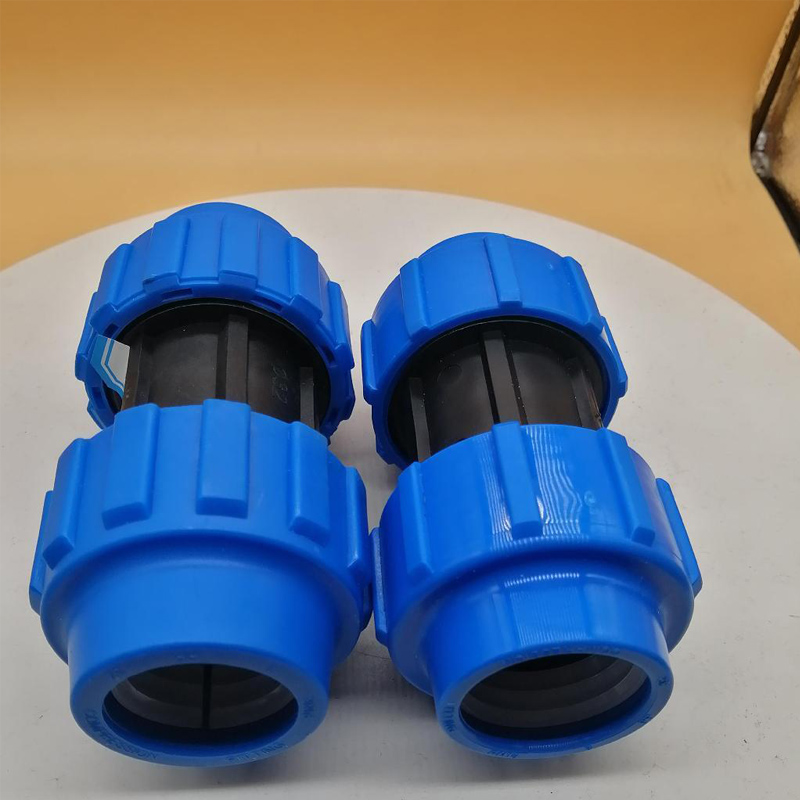
7. Real-World Application Case: Urban Water Supply Upgrade, Southeast Asia
- Minimize disruption and downtime
- Zero-leakage under fluctuating pressure
- Resilience to tropical humidity and aggressive disinfectants (chlorine, etc.)
- Long-term regulatory compliance (tested under Thai Metropolitan Waterworks Authority standards, 2023)
- Installation time reduced by 41% vs. welded joints
- <0.02% leak rate after six months (450+ pressure cycles)
- No reported cases of pipe assembly failure or water quality complaints
8. Application Scenarios and Dominant Advantages
Scenario | Advantage of DN25 HDPE compression fitting |
---|---|
Drinking Water Main | Certified for hygiene; no taste or odor impact |
Agricultural Irrigation | UV-stable; rapid assembly across large fields |
Industrial Chemicals | Superior chemical resistance, minimal leakage risk |
Repair & Retrofit | Working with old or multi-brand pipes—tool-free, adaptable assembly |
Mining/Slurry | Abrasion resistance saves cost on frequent replacements |
9. FAQ: Professional FAQ on DN25 HDPE Compression Fitting
PE100 is a high-performance grade of high-density polyethylene, providing maximum strength, crack resistance, and a longer service life (≥50 years). Its chemical stability is optimized for potable water and industrial fluids.
They are manufactured under ISO 4427, EN 12201, and ANSI/AWWA C906. Many are also WRAS certified for potable water use and meet RoHS/REACH environmental directives.
Standard max operating pressure is 16 bar; pressure/burst tested to above 48 bar (triple the working rating), verified as per EN/ISO protocols.
No special tools or solvent welding are required. Assembly is manual—simply insert the pipe, hand-tighten the compression nut, and tighten with a standard wrench as needed.
Yes, design is optimized for buried, direct-sun, and shaded installations, providing long-term leak-proof and corrosion-resistant performance.
Adapters are available to connect to steel (galvanized), copper, or PVC/PP pipes, facilitating retrofit or mixed-material networks.
For standard stock, delivery time is 3–5 days for bulk orders (FOB). Warranty ranges from 5 to 10 years, covering defects and performance failure.
10. Delivery, Warranty & Customer Care
- Delivery Time: 3–7 days for standard bulk orders. Expedited 48-hour service available upon request.
- Warranty: 5-10 years against material or process defects.
- Support: Free installation guides, tech support, and on-site troubleshooting (for projects).
- Traceability: Every DN25 HDPE compression fitting is batch-coded, with full quality records kept for 10+ years.
11. Additional Data Visualization
12. References & Further Reading
- HDPE Pipe Fittings Market to 2026 — Global Market Insights
- Latest ISO Standard Updates: ISO 4427: Polyethylene Pipes and Fittings
- Case Studies: Engineering Forums
- ScienceDirect Journal: "Performance of HDPE Compression Fittings Under Stress"
- HoronPipe Product Page: DN25 HDPE compression fitting