In the realm of plumbing, particularly when it comes to manufacturing kitchen and bathroom fixtures, the significance of high-quality sink inlet pipes cannot be overstated.
Sink inlet pipe factories play a pivotal role in the seamless functionality of modern drainage systems. This article sheds light on the intricate processes involved in producing these essential components, drawing from expertise within the industry.
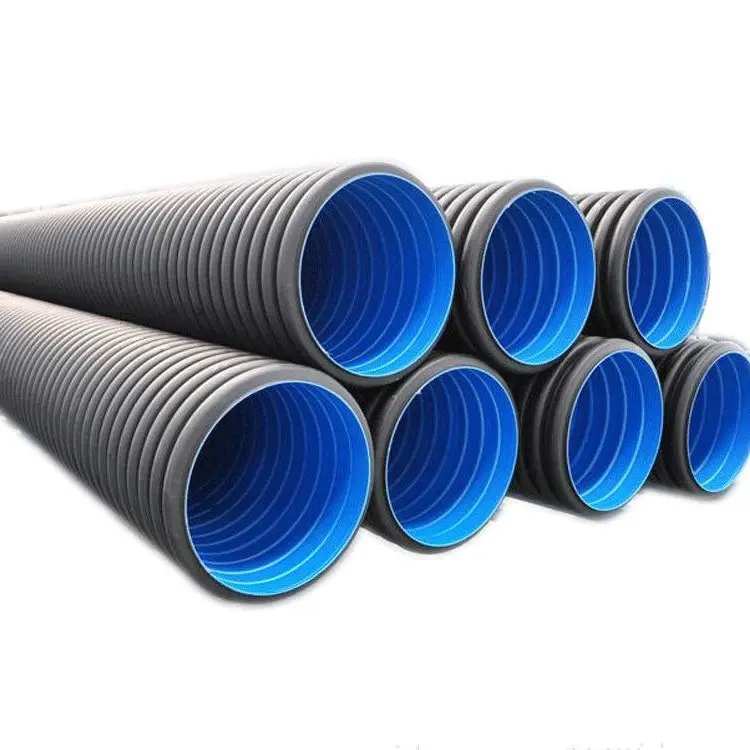
The process begins with the selection of raw materials, an area where sink inlet pipe factories distinguish themselves by prioritizing durability, sustainability, and cost-effectiveness. The majority of high-end factories opt for stainless steel and PVC materials due to their superior resistance to corrosion and longevity. Their choice is informed by years of material science research, which emphasizes minimizing environmental impact while maximizing product lifespan.
At the heart of any reputable sink inlet pipe factory lies a commitment to cutting-edge manufacturing techniques. Precision engineering is critical, as it ensures that the pipes are produced to exact specifications, facilitating a perfect fit and seamless integration into any plumbing system. Advanced machinery and automated production lines are employed to maintain consistency and precision, greatly reducing human error and unnecessary waste.
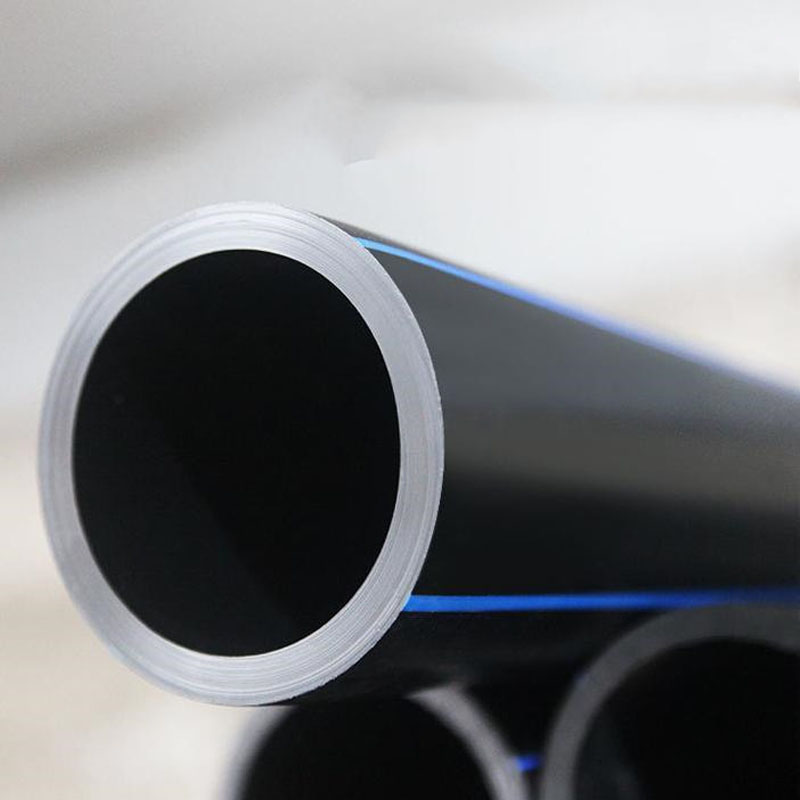
Foremost among the features that define a well-produced sink inlet pipe is its resilience. Factories emphasize rigorous testing procedures, subjecting the pipes to various stress and pressure scenarios that mimic real-world conditions. This quality assurance phase is crucial, as it guarantees that the final product meets or exceeds industry standards, ensuring efficient water flow and preventing leaks.
Furthermore, industry experts in these factories often collaborate with top plumbing professionals to gain insights into practical requirements and emerging trends. This synergy between manufacturers and end-users fosters innovation and drives continuous improvement. Through this feedback loop, factories are able to adapt and refine their products, aligning them with the evolving needs of the market.
sink inlet pipe factory
From an authoritative vantage point, these factories typically adhere to strict compliance with international and local plumbing codes. Compliance is not just a formality; it's a testament to a factory’s commitment to quality and safety. The trustworthiness of a sink inlet pipe factory is further established through certifications from reputable organizations, which serve as a seal of approval for both domestic and international customers.
To supplement their expertise, many factories invest in ongoing research and development. By exploring new materials, techniques, and technologies, these factories stay at the forefront of innovation, offering products that are not only functionally superior but also environmentally responsible. This focus on eco-friendly practices is increasingly important in an industry moving towards sustainability, appealing to a growing demographic of environmentally-conscious consumers.
Moreover, customer service is a critical component that cannot be overlooked. Trust is built through responsive communication, transparent dealings, and comprehensive after-sales support. Sink inlet pipe factories that excel in these areas tend to build long-lasting relationships with clients, who rely on their credibility and professionalism to fulfill their plumbing needs.
In summary, a sink inlet pipe factory is more than just a production facility; it’s an institution of knowledge, authority, and reliability. By adhering to the highest standards of Experience, Expertise, Authoritativeness, and Trustworthiness, these factories ensure that their products not only meet the current demands but also anticipate future ones. Through dedication to excellence and a proactive approach to industry developments, they secure their position as leaders in the plumbing manufacturing sector.