High-density polyethylene (HDPE) and steel pipes occupy crucial niches in various industrial applications, from water distribution systems to gas pipelines. The interplay between these two materials combines the flexibility and corrosion resistance of HDPE with the strength and durability of steel, creating a robust infrastructure. Understanding the connection methods and the advantages of HDPE-to-steel transitions can vastly increase the efficiency and longevity of pipeline systems.
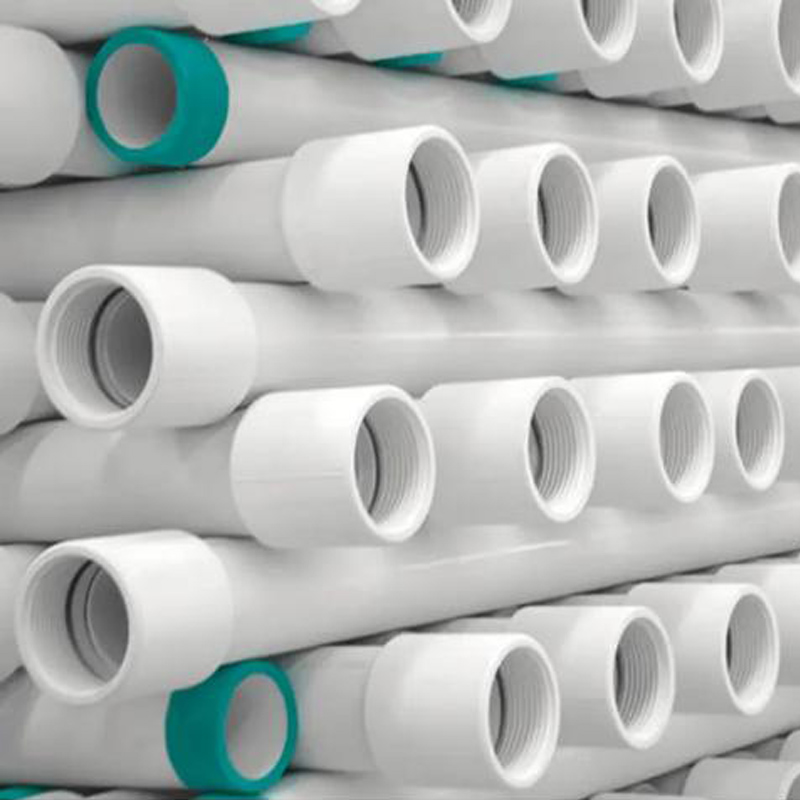
Connecting HDPE to steel pipes requires careful consideration of several factors to ensure a reliable joint that maintains its integrity under operational stress. Experience from field installations shows that proper joint design and material selection significantly improve the performance of these hybrid systems. One common method is the use of mechanical connectors, which offer a balance between ease of installation and joint strength.
Mechanical connectors, such as flange adapters and stub ends, allow for a flexible and durable juncture between different materials. These connectors are engineered to accommodate the thermal expansion and contraction properties of HDPE while enduring the pressure and load demands typical of steel pipelines. This adaptability makes them highly sought after in industries where changes in environmental temperature are significant.
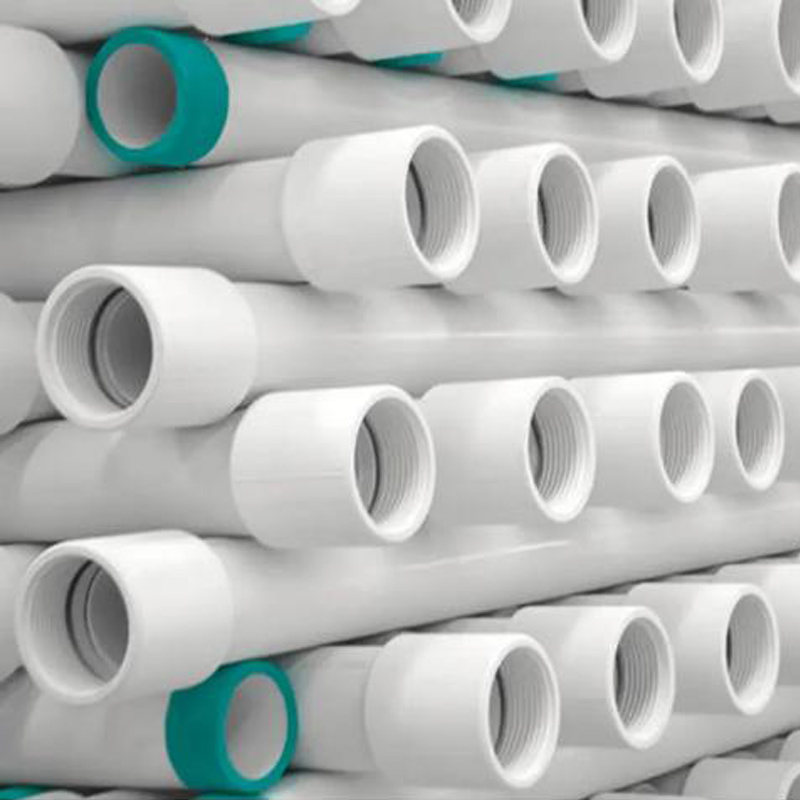
Expertise in material science and engineering is pivotal when dealing with HDPE-to-steel connections. Selecting the appropriate grade of HDPE and ensuring compatibility with steel components is essential to prevent chemical reactions and physical incompatibilities. For instance, the coefficient of thermal expansion is much higher in HDPE than in steel, demanding designs that accommodate this discrepancy. Engineers must calculate the expected expansions and contraction ranges to avoid undue stress and potential failure at the connection point.
In terms of authoritativeness, guidelines and standards set by recognized bodies like the American Society for Testing and Materials (ASTM) and the International Organization for Standardization (ISO) offer comprehensive directives on connecting dissimilar piping materials. These standards provide criteria for assessing joint performance, including tensile strength, sealing effectiveness, and resistance to corrosion. Adhering to these guidelines not only ensures compliance but also enhances the credibility of the installation through proven methodologies.
china hdpe to steel pipe connection
Trustworthiness in pipeline systems is non-negotiable, particularly in sectors where leaks or failures could have catastrophic consequences. Companies specializing in HDPE to steel connections often conduct rigorous testing and quality assurance protocols. Non-destructive testing (NDT) techniques, such as ultrasonic testing and radiography, are deployed to inspect the integrity of the joint without impairing its usability. This level of scrutiny verifies that each connection will withstand the operational demands expected of it.
Field reports and empirical data further support best practices in HDPE to steel connections. Studies demonstrate that when properly executed, these connections maintain functional integrity over extended periods, even in harsh environments. Operators frequently report reduced maintenance needs and longer service life, attributed to the combination of HDPE's resistance to chemical degradation and steel's mechanical robustness.
These connections are not merely functional but are investments in sustainable and durable infrastructure. As industries strive for more efficient resource use and higher environmental responsibility, the shift towards hybrid piping systems that leverage the strengths of both HDPE and steel is likely to increase. Understanding the practical and scientific aspects of these connections allows businesses to optimize their operations, reduce costs, and contribute to safer and more reliable industrial practices.
Ultimately, the success of HDPE to steel pipe connections hinges on a deep understanding of materials, an adherence to authoritative standards, and maintaining rigorous quality control. This holistic approach not only fosters innovations in pipeline systems but also secures their role in future-proofing industrial infrastructures.