An In-depth Look into Black HDPE Pipe Factories
High Density Polyethylene (HDPE) pipes, particularly the black variant, have become a staple in various industries due to their durability, chemical resistance, and cost-effectiveness. These pipes, primarily used for water supply, sewage systems, and gas transmission, are manufactured in numerous factories globally. This article delves into the world of black HDPE pipe production, highlighting key aspects of these factories.
Black HDPE pipes are preferred due to their inherent ability to resist UV rays, which makes them ideal for outdoor applications. The manufacturing process involves a combination of advanced technology, quality raw materials, and skilled labor. The primary raw material, high-density polyethylene resin, is sourced from reputable suppliers to ensure consistency and quality.
Factories dedicated to producing black HDPE pipes are typically equipped with state-of-the-art extrusion machines. These machines heat and mold the resin into the desired pipe shape and diameter. The process begins with the resin being fed into the extruder where it is melted and mixed. The molten plastic then passes through a die, forming the pipe's shape. As it exits the die, cooling water or air is applied to solidify the pipe, which is then cut to the required length.
Quality control is a crucial aspect in black HDPE pipe factories. Each pipe undergoes rigorous testing, including pressure tests, leak tests, and dimensional checks to ensure compliance with international standards such as ISO 4427 Each pipe undergoes rigorous testing, including pressure tests, leak tests, and dimensional checks to ensure compliance with international standards such as ISO 4427
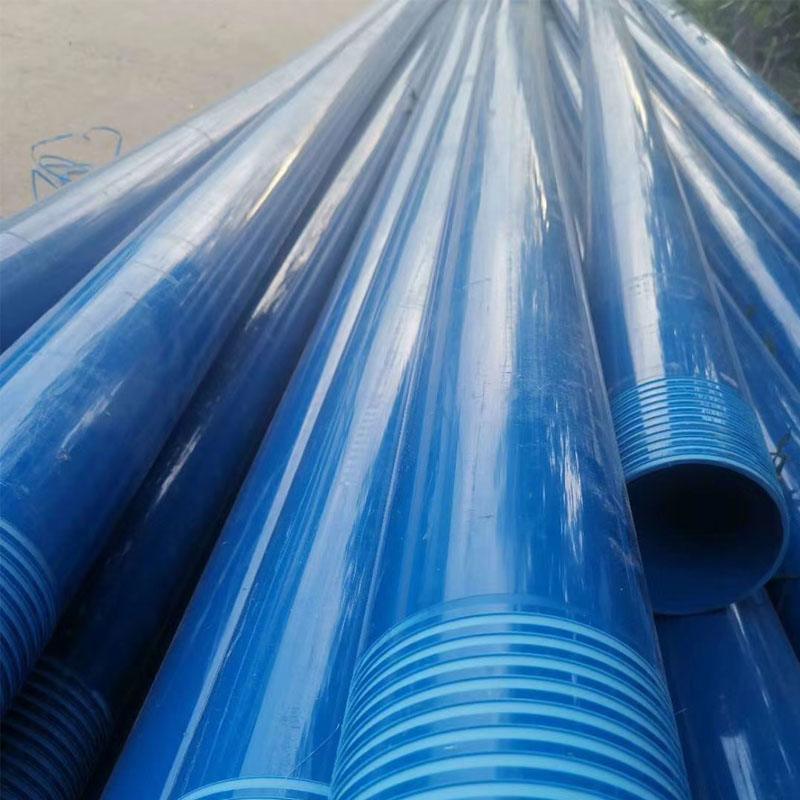
Each pipe undergoes rigorous testing, including pressure tests, leak tests, and dimensional checks to ensure compliance with international standards such as ISO 4427 Each pipe undergoes rigorous testing, including pressure tests, leak tests, and dimensional checks to ensure compliance with international standards such as ISO 4427
black hdpe pipe factories. Advanced inspection equipment and experienced technicians work together to guarantee that every pipe leaving the factory meets stringent quality benchmarks.
Moreover, sustainability is a growing concern in the industry, and black HDPE pipe factories are no exception. Many factories are adopting eco-friendly practices, such as recycling waste materials, reducing energy consumption, and using recyclable packaging. They also emphasize the longevity of HDPE pipes, which can last for decades without significant degradation, thus minimizing the need for frequent replacements.
In terms of global distribution, black HDPE pipe factories are strategically located around the world to cater to local and international markets. They often maintain strong partnerships with distributors and contractors to ensure timely delivery and efficient installation services.
The future of black HDPE pipe factories looks promising, as the demand for reliable and sustainable piping solutions continues to rise. With ongoing advancements in technology and a commitment to environmental responsibility, these factories are poised to play an increasingly vital role in infrastructure development worldwide.
In conclusion, black HDPE pipe factories represent a blend of technological sophistication, stringent quality control, and environmental consciousness. Their contribution to essential services like water supply and waste management is immense, making them a critical part of modern industrial ecosystems. As the world shifts towards more durable and eco-friendly solutions, the significance of these factories is set to grow even further.