Understanding HDPE Pipe Sizes and Their Impact on Service Efficiency
High-density polyethylene (HDPE) pipes are a crucial component in various industries, from municipal water supply and drainage systems to agricultural irrigation and chemical transportation. A thorough understanding of HDPE pipe sizes is essential for ensuring optimal service efficiency and longevity. This article delves into the importance of HDPE pipe dimensions and how they influence performance.
HDPE pipes come in a range of sizes, typically measured by their nominal diameter and pressure class. The nominal diameter, often expressed in inches or millimeters, does not represent the actual outside diameter but serves as a reference for fittings and connections. Pressure classes, such as PE 80 and PE 100, indicate the pipe's resistance to pressure, affecting its suitability for different applications.
Choosing the right size of HDPE pipe is paramount for maintaining flow rates and preventing unnecessary pressure losses. Undersized pipes can restrict flow, leading to increased pumping costs and potential system failures. Oversized pipes, on the other hand, may result in higher material and installation expenses without providing commensurate benefits. Therefore, accurate sizing calculations that consider factors like fluid type, flow rate, and expected growth are vital.
In addition to diameter and pressure class, wall thickness also plays a significant role in determining a pipe's strength and flexibility
In addition to diameter and pressure class, wall thickness also plays a significant role in determining a pipe's strength and flexibility
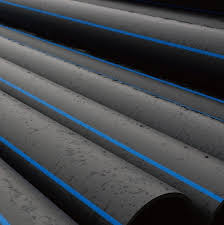
In addition to diameter and pressure class, wall thickness also plays a significant role in determining a pipe's strength and flexibility
In addition to diameter and pressure class, wall thickness also plays a significant role in determining a pipe's strength and flexibility
hdpe pipe sizes service. Thicker walls provide greater resistance to external forces and offer better protection against impact damage. However, they also increase the weight and cost of the pipe. Balancing these factors is crucial for selecting an HDPE pipe that meets the specific needs of a project.
Furthermore, the joining method used between HDPE pipes can influence overall system efficiency. Heat fusion, electrofusion, and butt fusion are common techniques that create leak-proof joints. Proper installation ensures that the piping system maintains its integrity over time, preventing costly leaks and extending the service life of the pipeline.
In conclusion, the correct selection and installation of HDPE pipes based on their sizes and pressure ratings are fundamental to achieving reliable and efficient service. By considering factors such as diameter, pressure class, wall thickness, and joining methods, engineers and contractors can design systems that optimize performance while minimizing costs. As technology advances and materials improve, it is imperative to stay informed about the latest developments in HDPE pipe sizing to continue enhancing service efficiency across various sectors.