High-Density Polyethylene (HDPE) piping systems are widely favored for their durability, flexibility, and resistance to corrosion, making them an excellent choice in various applications, from water supply to industrial piping. One crucial component of these systems is the HDPE coupler. Whether you’re looking to connect HDPE pipes or ensure the seamless flow in an existing setup, knowing about HDPE couplings and finding a reliable HDPE coupler manufacturer can make a significant difference.
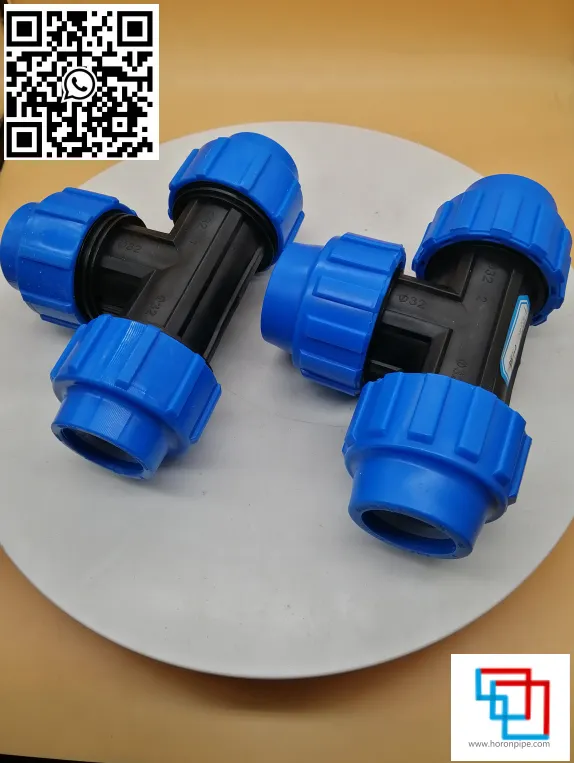
What Are HDPE Couplings?
HDPE couplings are connectors designed to join two pieces of HDPE pipe. They are essential for ensuring that piping systems are stable, leak-free, and capable of handling high pressure without deterioration. HDPE couplings can come in various forms, including mechanical couplings, electrofusion couplings, and compression couplings, each tailored to specific application requirements.
Types of HDPE Pipe Couplings
Mechanical Couplings:
- These are easy-to-install couplings that provide a tight, secure connection without the need for welding. Mechanical couplings are typically used for temporary connections or in areas where frequent dismantling is needed.
Electrofusion Couplings:
- Electrofusion couplings are connected to HDPE pipes using a special electrofusion welding process, providing a more permanent, leak-resistant connection. They are ideal for critical infrastructure and high-pressure applications.
Compression Couplings:
- Compression couplings use compression rings to tightly connect HDPE pipes. These are popular in applications like irrigation, as they provide a secure connection without specialized tools.
Butt Fusion Couplings:
- Butt fusion involves heating the ends of two HDPE pipes and pressing them together to form a single continuous pipe. It’s a method used for long-lasting connections in buried pipelines.
Choosing a Reliable HDPE Coupler Manufacturer
Selecting the right HDPE coupler manufacturer is crucial to ensure product quality, longevity, and performance. Here’s what to look for when evaluating manufacturers:
Quality Standards and Certifications:
- Look for manufacturers that adhere to industry standards and certifications, such as ISO certifications, to ensure high-quality, durable products. Manufacturers that follow these standards are more likely to provide reliable couplers that meet rigorous safety and performance requirements.
Experience and Expertise:
- A reputable HDPE coupler manufacturer should have a solid track record and in-depth knowledge of HDPE materials, fabrication techniques, and coupling solutions. Experienced manufacturers often produce a range of couplings to meet specific industry demands.
Product Range:
- A good manufacturer will offer a variety of coupling options, including HDPE pipe couplings, compression couplings, electrofusion couplings, and more. This variety demonstrates their understanding of diverse project needs and their ability to supply tailored solutions.
Customization:
- Customization can be essential for large-scale or specialized projects. Many high-quality manufacturers offer custom-sized couplings and can accommodate unique specifications for project-specific requirements.
Support and Services:
- A reliable manufacturer offers technical support, installation guidance, and after-sales services. They understand that successful installation and proper maintenance are critical to long-term performance, and they support clients through every phase of the project.
Understanding HDPE Pipe Coupler Price
HDPE pipe coupler prices can vary significantly based on factors like size, type, material grade, and the coupling technique. Here’s what influences the pricing:
Material Grade:
- Higher-grade materials, designed for high-pressure or critical applications, are more expensive but offer enhanced durability and performance. Low-grade materials might cost less but could have shorter lifespans and lower resistance to environmental factors.
Type of Coupling:
- Electrofusion and butt fusion couplings generally have a higher price due to the complexity of the connection process and the high-strength bond they provide. Compression couplings are often more affordable and suitable for less demanding applications.
Size of Coupler:
- Larger couplers cost more due to the increased amount of HDPE material required in their manufacture. Large-diameter HDPE pipes used in industrial applications typically need heavy-duty couplings, which can further increase costs.
Manufacturer and Brand Reputation:
- Premium brands with established reputations may charge more for their products due to quality assurance, certifications, and reliable performance records. However, investing in a trusted brand often results in longer-lasting installations and fewer maintenance issues.
Market and Order Volume:
- Ordering HDPE couplers in bulk often reduces the per-unit cost, making it more economical for large-scale projects. Additionally, certain market conditions, such as demand fluctuations, can influence pricing.
Benefits of Investing in High-Quality HDPE Couplings
High-quality HDPE couplings offer numerous benefits, especially in terms of performance, durability, and cost-efficiency:
Leak Prevention:
- Properly installed HDPE couplings minimize the risk of leaks, ensuring that systems remain efficient and minimizing potential hazards or costly repairs.
Long Lifespan:
- HDPE couplings are highly resistant to corrosion, abrasion, and chemical damage, making them suitable for both outdoor and underground installations. A high-quality coupling will last for years with minimal maintenance.
Reduced Maintenance:
- With reliable, durable couplings, systems require less maintenance, reducing downtime and associated costs. High-quality couplings stand up well to temperature fluctuations and environmental stress.
Environmentally Friendly:
- HDPE is a recyclable material, making HDPE couplings an environmentally friendly choice. By choosing long-lasting couplings, you’re also reducing waste from frequent replacements.
Investing in the right HDPE coupler manufacturer and understanding HDPE pipe coupling options are essential steps to building a robust, durable, and efficient piping system. From temporary solutions to permanent installations, selecting the correct type of coupling can enhance your system's performance, reduce downtime, and support safe and seamless operation.