The Role of Couplers in HDPE Pipe Applications
In the realm of polyethylene piping systems, high-density polyethylene (HDPE) pipes stand out for their exceptional durability and resistance to corrosion. However, the effectiveness of an HDPE pipeline system is not only determined by the quality of the pipe material but also by the integrity of its connections. This is where couplers for HDPE pipes come into play, ensuring secure and reliable joints between pipe sections.
A coupler, also known as a coupling or fitting, serves as a critical component that links two HDPE pipes together. These devices are designed with a female socket at both ends, allowing the insertion of the pipe ends and forming a tight, pressure-resistant seal. The use of couplers is paramount in situations where direct butt fusion or electrofusion might not be feasible or practical, such as in complex installations or when repairs are needed in existing pipelines without cutting the entire length of pipe.
The design of HDPE couplers typically incorporates a rubber gasket or seal to prevent leakage. When properly installed, these couplers provide a mechanical connection that can withstand significant pressure and environmental stresses. Moreover, they offer flexibility in terms of expansion and contraction due to temperature changes, a crucial factor in preventing joint failure over time.
Manufacturers have developed specialized couplers for various applications, including those suitable for above-ground or underground utilities, potable water supply, sewage disposal, and chemical transport
Manufacturers have developed specialized couplers for various applications, including those suitable for above-ground or underground utilities, potable water supply, sewage disposal, and chemical transport
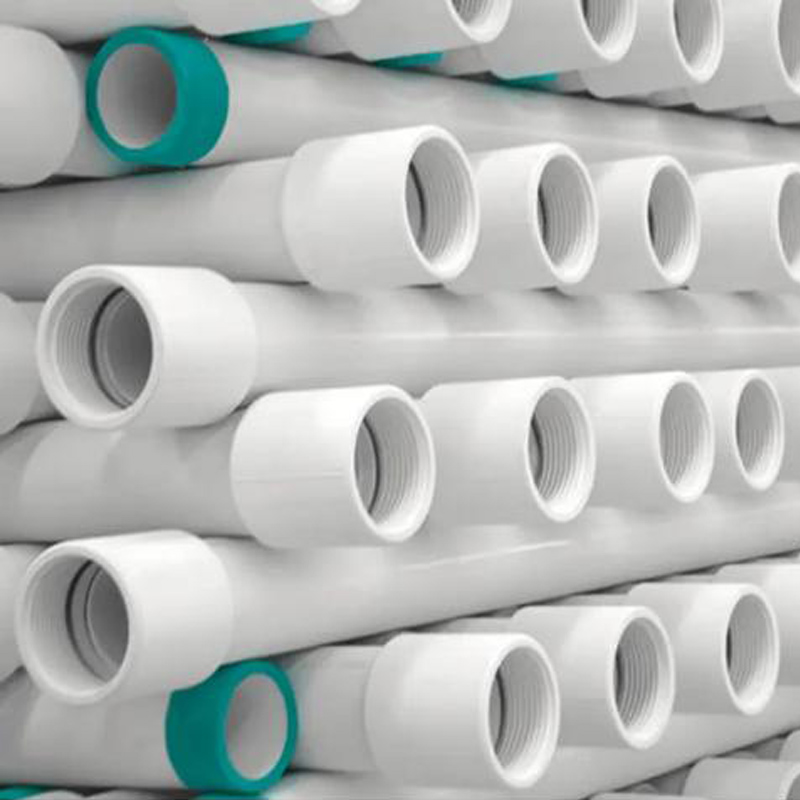
Manufacturers have developed specialized couplers for various applications, including those suitable for above-ground or underground utilities, potable water supply, sewage disposal, and chemical transport
Manufacturers have developed specialized couplers for various applications, including those suitable for above-ground or underground utilities, potable water supply, sewage disposal, and chemical transport
coupler for hdpe pipe product. For example, couplers used in pressurized water systems often feature stainless steel clamps for added security against high water pressure. Meanwhile, those intended for non-pressurized drainage systems may rely solely on the snug fit and sealing properties of the gasket.
In the construction of HDPE pipelines, the selection and installation of appropriate couplers cannot be overlooked. Engineers and technicians must consider factors such as the diameter and pressure rating of the pipes, the type of fluid being transported, and the specific environmental conditions of the installation site. Properly chosen and installed couplers ensure that the pipeline remains leak-free, reducing maintenance costs and extending the lifespan of the system.
In conclusion, while the robustness of HDPE pipes is well-documented, it is the unsung heroes like the couplers that ensure the seamless operation of these pipeline systems. As connectors between HDPE pipe segments, couplers embody the principle of strength through unity, safeguarding the flow of resources and protecting the integrity of vital infrastructure. By recognizing the importance of these components, we can better appreciate the engineering behind efficient and reliable piping networks.